Home>Misc>Featured>What Document Outlines The Health And Safety Related Procedures Programs Follow?
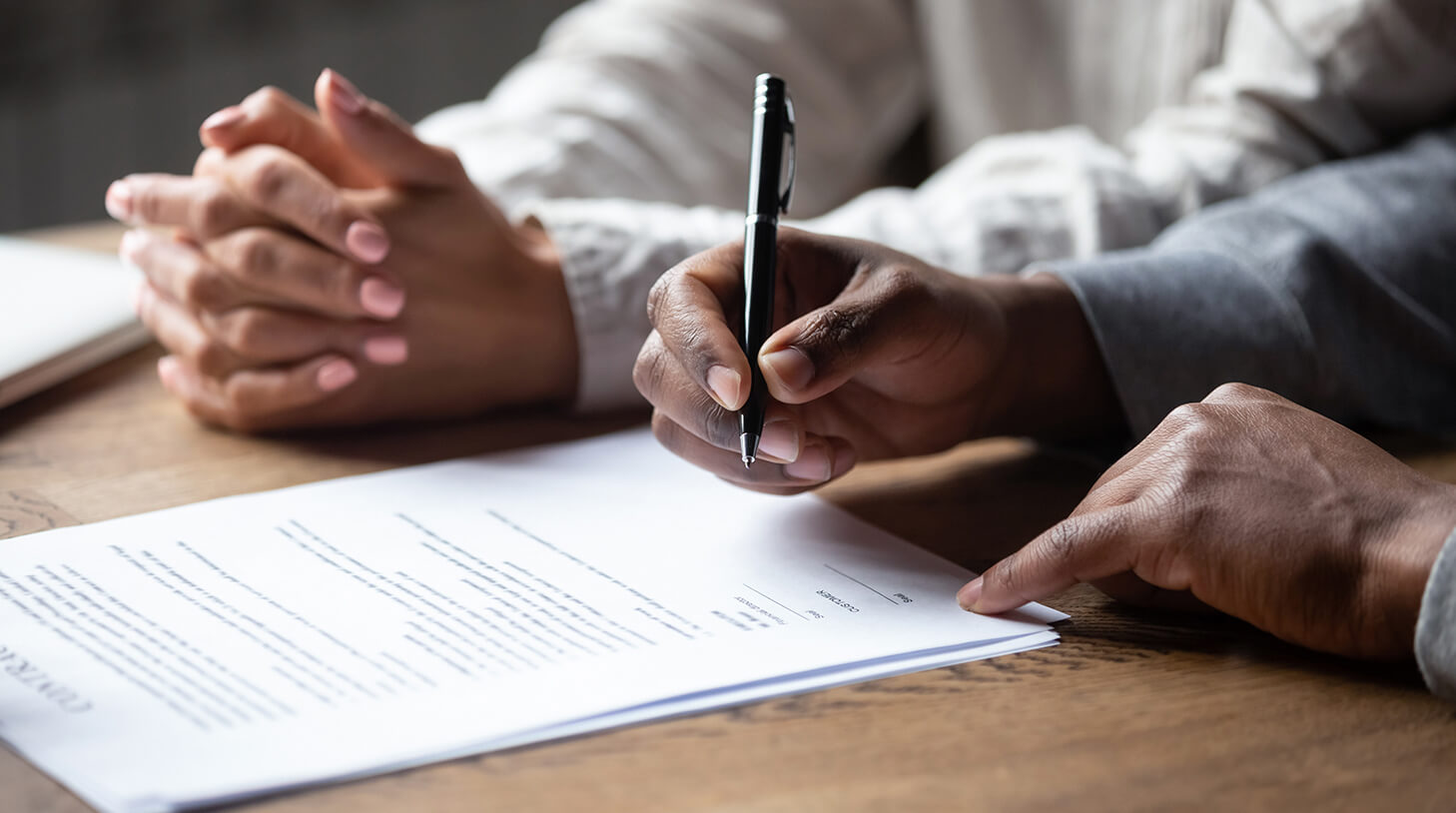
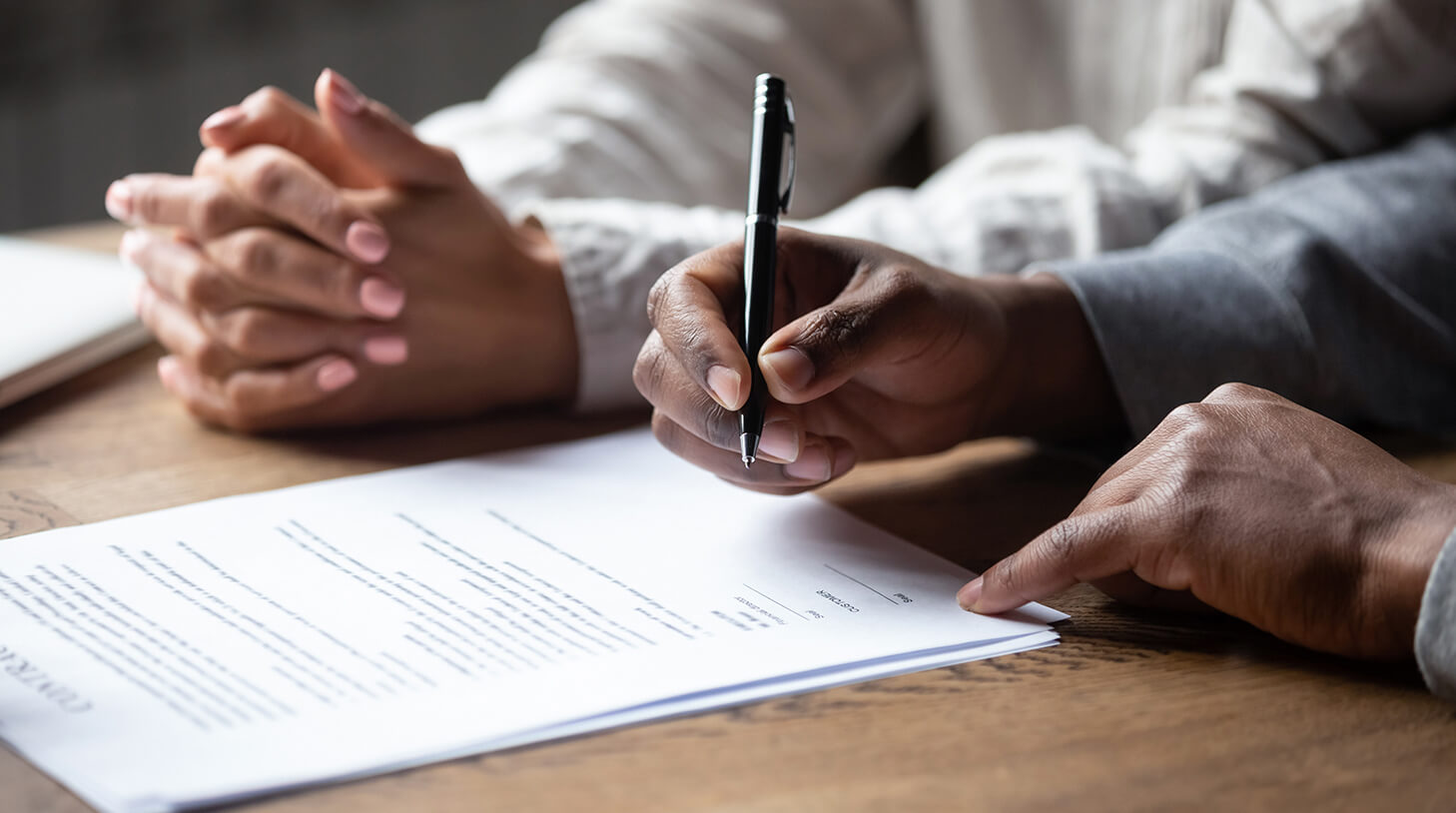
Featured
What Document Outlines The Health And Safety Related Procedures Programs Follow?
Published: September 9, 2023
Discover the featured document that outlines the health and safety procedures and programs followed by organizations. Ensure a safe working environment for all staff.
Introduction
When it comes to ensuring a safe and healthy work environment, organizations must have proper procedures and programs in place. These procedures and programs outline the necessary steps to assess, control, and manage potential hazards in the workplace. But what exactly documents these health and safety-related procedures and programs? Let’s dive into the world of occupational health and safety to find out.
Workplaces can be filled with various risks and hazards, and it is the responsibility of employers to protect their employees from harm. This is not only a legal requirement, but it also promotes a culture of safety and well-being within the organization. The cornerstone legislation governing health and safety in the United States is the Occupational Safety and Health (OSH) Act.
The OSH Act was enacted in 1970 and aims to ensure safe and healthful working conditions for employees across the country. Under this act, the Occupational Safety and Health Administration (OSHA) was established to enforce standards and regulations related to workplace safety. These federal regulations and standards provide a framework for organizations to follow in order to maintain a safe work environment.
While the OSH Act and federal regulations set the foundation for workplace safety, individual organizations need to develop their own Health and Safety Program Document that outlines their specific procedures and programs. This document serves as a comprehensive guide for employees and management to understand the steps to take when it comes to identifying, assessing, controlling, and managing hazards in the workplace.
The Health and Safety Program Document is a crucial tool for organizations as it not only outlines the procedures and programs to be followed, but also helps in creating a culture of safety by promoting awareness and accountability. By having a documented program, organizations can ensure that all employees are aware of the steps to be taken in case of an emergency, understand the potential risks in their work environment, and are equipped with the necessary information and training to prevent accidents and injuries.
In the following sections, we will explore the key elements that are typically included in a Health and Safety Program Document, including procedures for hazard identification and assessment, hazard control and management, emergency response and preparedness, employee training and communication, incident reporting and investigation, as well as auditing and evaluation procedures.
Importance of Health and Safety Procedures
Health and safety procedures are essential in any workplace, regardless of industry or size. These procedures provide a systematic approach to identifying and mitigating potential hazards, protecting the well-being of employees, and ensuring compliance with legal requirements. Let’s explore the importance of health and safety procedures in more detail.
1. Employee Safety: The primary goal of health and safety procedures is to ensure the safety and well-being of employees. By implementing procedures, organizations can identify and assess potential hazards, such as unsafe working conditions or equipment, and take proactive measures to control and manage these risks. This reduces the likelihood of accidents, injuries, and occupational illnesses, creating a safer work environment for all employees.
2. Legal Compliance: Compliance with health and safety regulations is not only a moral obligation but also a legal requirement. Failure to adhere to these regulations can result in heavy fines, legal liabilities, damage to the organization’s reputation, and potential legal action. By implementing and following health and safety procedures, organizations can demonstrate their commitment to complying with these regulations, reducing the risk of penalties and legal consequences.
3. Increased Productivity: A safe and healthy work environment promotes productivity among employees. When employees feel safe, they can focus on their tasks without the distraction or fear of potential hazards. Health and safety procedures help create a positive work culture and improve employee morale, leading to increased productivity and better overall job satisfaction.
4. Cost Reduction: Workplace accidents and injuries can have significant financial implications for organizations. Medical expenses, workers’ compensation claims, equipment damage, and productivity losses due to employee absences or reduced efficiency can all result in substantial costs. By implementing effective health and safety procedures, organizations can reduce the frequency and severity of accidents, minimizing these financial burdens.
5. Reputation and Stakeholder Confidence: Organizations that prioritize health and safety not only protect their employees but also enhance their reputation and stakeholder confidence. Customers, clients, investors, and business partners are more likely to trust and engage with organizations that prioritize employee well-being. Additionally, a positive reputation for safety can attract top talent, leading to a skilled and motivated workforce.
Overall, health and safety procedures are vital for protecting employees, ensuring legal compliance, promoting productivity, reducing costs, and enhancing the organization’s reputation. By implementing and following these procedures, organizations can create a safe and positive work environment, fostering a culture of safety and well-being for all.
The Occupational Safety and Health Act (OSH Act)
The Occupational Safety and Health (OSH) Act serves as the foundation for workplace safety regulations in the United States. Enacted in 1970, the OSH Act establishes guidelines and standards to ensure safe and healthful working conditions for employees across various industries. Let’s take a closer look at the key aspects of the OSH Act and its significance in protecting workers.
The primary objective of the OSH Act is to prevent work-related injuries, illnesses, and fatalities by promoting safe working conditions. It places responsibility on employers to provide a workplace free from recognized hazards that may cause serious harm or death to workers. The act empowers the Occupational Safety and Health Administration (OSHA) to enforce compliance with these requirements.
Under the OSH Act, OSHA is responsible for a range of activities, including establishing and enforcing workplace safety standards, conducting inspections of workplaces, investigating complaints and accidents, providing training and education, and promoting voluntary compliance with safety regulations. OSHA has the authority to issue citations and penalties for violations of safety standards, ensuring that employers prioritize the health and well-being of their employees.
By establishing legal rights and responsibilities for both employers and employees, the OSH Act helps to create a culture of safety in the workplace. Employers are required to provide employees with a workplace free from recognized hazards, complying with OSHA standards and regulations. Employees, on the other hand, have the right to request workplace inspections, file complaints regarding unsafe conditions, and participate in the development of safety programs.
One important provision of the OSH Act is the General Duty Clause, which states that employers must furnish a workplace free from recognized hazards that are causing or are likely to cause death or serious physical harm to employees. This provision ensures that employers take proactive measures to identify and address workplace hazards that may not be specifically covered by OSHA standards.
The OSH Act covers most private-sector employers and employees in the United States, with a few exceptions such as self-employed individuals, family farms, and workplaces already regulated by other federal agencies. To ensure compliance, OSHA conducts inspections based on industry classification, the severity of the hazard, previous violations, and employee complaints.
Overall, the OSH Act plays a crucial role in safeguarding the well-being of workers across the country. It establishes the legal framework for workplace safety and empowers OSHA to enforce safety standards. By prioritizing the health and safety of employees, the OSH Act contributes to reducing workplace accidents, injuries, and illnesses, creating a safer and healthier work environment.
Federal Regulations and Standards
In addition to the Occupational Safety and Health (OSH) Act, there are various federal regulations and standards that govern workplace safety in the United States. These regulations and standards provide specific guidelines and requirements that employers must follow to ensure the health and safety of their employees. Let’s delve deeper into the significance of federal regulations and standards in maintaining safe working conditions.
The Occupational Safety and Health Administration (OSHA), established under the OSH Act, is responsible for developing and enforcing these federal regulations and standards. OSHA’s primary objective is to prevent workplace injuries, illnesses, and fatalities by setting clear guidelines for employers to follow.
OSHA regulations cover a wide range of industries and work environments, including but not limited to construction, manufacturing, healthcare, and transportation. These regulations address various aspects of workplace safety, such as hazard communication, fall protection, electrical safety, machine guarding, personal protective equipment (PPE), and more.
Employers are required to familiarize themselves with the relevant OSHA regulations applicable to their industry and ensure compliance in their workplaces. Failure to comply with these regulations can result in citations, penalties, and legal consequences.
OSHA standards, on the other hand, provide specific requirements and recommendations for safe work practices. These standards are aimed at reducing the risk of injuries and illnesses by providing a baseline level of protection for employees.
OSHA standards cover a wide range of topics, including but not limited to respiratory protection, hazardous materials handling, ergonomic practices, noise exposure, and machine safety. Employers are responsible for identifying the applicable standards to their operations and implementing measures to comply with them.
To facilitate compliance, OSHA provides resources such as guidelines, training materials, and consultation services to help employers understand and implement the regulations and standards effectively.
In addition to OSHA regulations, there are other federal agencies that enforce specific safety regulations for certain industries. For example, the Mine Safety and Health Administration (MSHA) enforces safety standards for mining operations, while the Federal Aviation Administration (FAA) regulates safety in the aviation industry.
Overall, federal regulations and standards play a critical role in ensuring workplace safety across the country. They provide guidelines that employers must follow to protect their employees from hazards and maintain a safe working environment. Adherence to these regulations not only prevents accidents and injuries but also fosters a culture of safety within organizations.
The Health and Safety Program Document
The Health and Safety Program Document is a comprehensive guide that outlines the specific procedures and programs an organization follows to ensure a safe and healthy work environment. It serves as a roadmap for employees and management, detailing the necessary steps to identify, assess, control, and manage potential hazards in the workplace. Let’s explore the significance of the Health and Safety Program Document in more detail.
The Health and Safety Program Document is a vital tool for organizations as it establishes a framework for implementing effective health and safety practices. This document is typically developed by the organization’s health and safety team or specialist, in collaboration with management and employees.
The primary purpose of the Health and Safety Program Document is to provide guidance to employees on how to prioritize their safety and well-being. It outlines the protocols, procedures, and programs in place to maintain a safe work environment, promoting a culture of safety throughout the organization.
Moreover, the Health and Safety Program Document helps organizations meet legal requirements related to health and safety. It ensures that proper procedures are in place to comply with federal regulations and standards set by organizations such as the Occupational Safety and Health Administration (OSHA).
The document typically includes various elements, such as hazard identification and assessment procedures, hazard control and management procedures, emergency response and preparedness procedures, employee training and communication procedures, incident reporting and investigation procedures, as well as auditing and evaluation procedures. These elements together create a comprehensive approach to managing workplace safety.
By having a documented program, organizations can ensure that all employees are aware of their responsibilities and obligations when it comes to health and safety. It helps employees understand the potential risks in their work environment and the steps they need to take to protect themselves and their colleagues.
The Health and Safety Program Document also provides a mechanism for continuous improvement. It allows organizations to review and update their procedures based on evolving regulations, industry best practices, and the lessons learned from incidents or near misses. Regular evaluations of the program’s effectiveness help identify areas for improvement and ensure that the organization remains proactive in maintaining a safe work environment.
Overall, the Health and Safety Program Document serves as a roadmap for organizations to promote a culture of safety, meet legal requirements, and protect the well-being of their employees. It provides clear guidelines and procedures that help prevent accidents, injuries, and occupational illnesses, creating a safer and healthier workplace for all.
Elements of a Health and Safety Program
A comprehensive and effective Health and Safety Program is crucial for maintaining a safe and healthy work environment. It consists of various elements that work together to identify, assess, control, and manage potential hazards in the workplace. Let’s explore the key elements of a Health and Safety Program in more detail.
1. Hazard Identification and Assessment: This element involves conducting regular inspections and assessments to identify potential hazards in the workplace. It includes identifying physical hazards, such as machinery or chemical substances, as well as evaluating environmental factors, like noise levels or ventilation. This step helps organizations gain a thorough understanding of the risks present in their work environment.
2. Hazard Control and Management: Once hazards are identified, the next step is to implement control measures to mitigate the risks. This element focuses on strategies and procedures to eliminate or minimize hazards. It includes implementing engineering controls, such as installing safety guards, providing personal protective equipment (PPE), establishing safe work practices, and developing standard operating procedures.
3. Emergency Response and Preparedness: This element outlines the procedures and protocols to be followed in case of emergencies, such as fires, chemical spills, or medical incidents. It includes developing evacuation plans, establishing emergency communication systems, providing first aid training, and ensuring the availability of necessary emergency equipment.
4. Employee Training and Communication: Proper training and effective communication are essential for promoting a culture of safety within an organization. This element focuses on providing comprehensive health and safety training to employees, ensuring that they understand the potential hazards, know how to use safety equipment, and are aware of the procedures to follow in different situations. Regular communication channels are established to keep employees informed about safety updates, new procedures, and any changes in regulations.
5. Incident Reporting and Investigation: Accurate and timely reporting of incidents or near misses is crucial for identifying root causes, implementing corrective actions, and preventing future occurrences. This element includes establishing an incident reporting system, conducting thorough investigations to determine causes, and implementing preventive measures to avoid similar incidents in the future.
6. Auditing and Evaluation: Regular auditing and evaluation of the Health and Safety Program ensure its ongoing effectiveness. This element involves conducting internal audits, reviewing safety performance, measuring key indicators, and reassessing risk assessments. It helps identify areas for improvement and ensures compliance with regulations and standards.
These elements work together to create a comprehensive Health and Safety Program that promotes a safe and healthy work environment. Each element is crucial in addressing different aspects of workplace safety, from hazard identification to employee training and incident response. By implementing a well-rounded Health and Safety Program, organizations can protect their employees, prevent accidents and occupational illnesses, and foster a culture of safety.
Procedures for Identifying and Assessing Hazards
Identifying and assessing hazards is a critical component of any effective health and safety program. These procedures help organizations understand the potential risks present in the workplace and take appropriate measures to control and manage those hazards. Let’s explore the key procedures involved in identifying and assessing hazards in more detail.
1. Regular Inspections: Conducting regular inspections is essential for identifying potential hazards. These inspections can be carried out by trained personnel, supervisors, or dedicated health and safety teams. Inspections should encompass all areas of the workplace, including workstations, equipment, materials, ventilation systems, and storage areas.
2. Employee Participation: Involving employees in the hazard identification process is crucial. They are often the ones who have firsthand knowledge of potential hazards in their work areas. Encouraging employees to report and communicate about potential hazards through open dialogues, suggestion boxes, or anonymous reporting systems helps in identifying hazards that may otherwise go unnoticed.
3. Job Hazard Analysis (JHA): Job hazard analysis involves breaking down individual job tasks and assessing the potential hazards associated with each task. This systematic approach enables organizations to identify specific hazards and develop appropriate preventive measures and controls. JHA should consider factors such as equipment usage, environmental conditions, ergonomics, and potential interactions between tasks.
4. Documentation and Record-Keeping: Effective hazard identification and assessment procedures involve maintaining proper documentation and records. These records can include inspection reports, incident reports, employee hazard reports, and completed job hazard analyses. Regularly reviewing and updating these records helps organizations track their progress in identifying and addressing hazards.
5. Risk Assessment: Once hazards are identified, conducting risk assessments helps gauge the severity and potential impact of those hazards. Risk assessments consider factors such as the likelihood of an incident occurring, the potential consequences, and the level of exposure for employees. This information enables organizations to prioritize hazards and allocate resources effectively for controlling and managing risks.
6. Use of Technology and Tools: Technology can aid in identifying and assessing hazards. Organizations can use tools such as digital inspection checklists, risk assessment software, and hazard mapping technologies to streamline the process. These tools allow for efficient data collection, analysis, and reporting, ensuring a more systematic and comprehensive approach to hazard identification and assessment.
7. Training and Education: Proper training and education of employees are vital for effective hazard identification and assessment. Providing employees with the necessary knowledge and skills helps them recognize and report hazards promptly. Training can be focused on hazard recognition, reporting procedures, and the importance of hazard control.
By following these procedures, organizations can proactively identify and assess potential hazards in the workplace. This enables them to take necessary preventive measures, establish appropriate controls, and ensure the safety and well-being of their employees. Regular review and updating of hazard identification and assessment procedures are essential to keep up with evolving hazards and changing work conditions.
Procedures for Controlling and Managing Hazards
Controlling and managing hazards is a critical aspect of maintaining a safe and healthy work environment. Organizations must have robust procedures in place to mitigate or eliminate potential risks. These procedures ensure that appropriate measures are taken to control hazards effectively. Let’s explore the key procedures involved in controlling and managing hazards in more detail.
1. Engineering Controls: One of the most effective ways to control hazards is through engineering controls. This involves modifying or redesigning work processes, equipment, or systems to eliminate or minimize exposure to the hazard. Examples of engineering controls include installing machine guards, providing adequate ventilation, or implementing noise reduction measures.
2. Administrative Controls: Administrative controls focus on implementing policies, procedures, and work practices to reduce exposure to hazards. This may include implementing rotation of tasks to limit exposure time, enforcing safe work procedures, providing proper training on hazard controls, and establishing clear safety policies. Administrative controls help establish guidelines and expectations for employees, ensuring that they understand the protocols and procedures for maintaining a safe work environment.
3. Personal Protective Equipment (PPE): When hazards cannot be eliminated or controlled through engineering or administrative controls, the use of personal protective equipment becomes essential. PPE includes items such as gloves, safety glasses, hard hats, respiratory protection, and hearing protection. Procedures for controlling and managing hazards should include guidelines on selecting, using, and maintaining appropriate PPE, as well as training employees on proper PPE usage.
4. Hazard Communication: Effective communication regarding hazards is crucial for their control and management. Procedures should include clear communication channels to inform employees about potential hazards, their associated risks, and control measures in place. This can be achieved through safety training programs, safety data sheets, warning signs and labels, and regular updates on changes to hazards or control measures.
5. Maintenance and Inspections: Regular maintenance and inspections are necessary to ensure that control measures are functioning effectively. Procedures should outline specific schedules for equipment maintenance and inspections. This includes checking for worn-out or damaged safety equipment, conducting preventive maintenance, and addressing any identified hazards promptly.
6. Emergency Response Plans: Hazard control procedures should also include the development and implementation of emergency response plans. These plans outline the steps to be taken in the event of an emergency or incident, such as fire, chemical spill, or workplace violence. Procedures should include training employees on emergency response procedures, evacuation routes, assembly points, and communication protocols.
7. Continuous Monitoring and Improvement: Controlling and managing hazards is an ongoing process that requires regular monitoring and evaluation. Procedures should include mechanisms for monitoring the effectiveness of control measures, conducting audits, and gathering feedback from employees. This allows organizations to identify areas for improvement and adjust control measures as needed.
By following these procedures, organizations can effectively control and manage hazards in the workplace. Implementing engineering controls, administrative controls, and proper use of PPE, along with effective hazard communication and emergency response plans, helps minimize the risk of accidents and injuries. Regular monitoring and continuous improvement ensures that control measures remain effective in mitigating hazards and maintaining a safe work environment.
Emergency Response and Preparedness Procedures
Emergency response and preparedness procedures are crucial for ensuring the safety and well-being of employees in the event of unexpected events or disasters. Organizations must have well-defined procedures in place to effectively respond to emergencies and mitigate potential risks. Let’s explore the key procedures involved in emergency response and preparedness in more detail.
1. Emergency Action Plan (EAP): An Emergency Action Plan is a critical component of emergency response and preparedness. It outlines the specific actions to be taken in various emergency situations, such as fires, natural disasters, chemical spills, or workplace violence incidents. The plan should include evacuation procedures, emergency contacts, assembly points, and clear communication protocols.
2. Emergency Evacuation Procedures: Clear and effective evacuation procedures are essential for ensuring the safe and orderly evacuation of employees during emergencies. These procedures should outline evacuation routes, assembly areas, and the specific roles and responsibilities of designated personnel (e.g., floor wardens or fire marshals) who will assist in evacuating employees. Regular drills and training sessions should also be conducted to familiarize employees with the evacuation procedures and routes.
3. Emergency Communication Systems: Establishing reliable communication systems is vital during emergencies to ensure that employees receive timely and accurate information. This may include setting up a public address system, emergency alarms, or other means of communication such as text messages or email alerts. Procedures should include clear instructions on how to use these communication systems effectively during an emergency and how to disseminate important information to employees.
4. First Aid and Medical Assistance: Procedures for emergency response and preparedness should include guidelines for providing first aid and obtaining medical assistance during emergencies. This involves training employees in basic first aid skills, ensuring the availability of first aid kits and emergency medical supplies, and designating individuals who are trained in CPR and other life-saving techniques.
5. Shelter-in-Place Procedures: In some emergencies, such as chemical spills or severe weather conditions, it may be necessary for employees to shelter-in-place rather than evacuate. Procedures should outline the steps to be taken in such situations, including moving to designated safe areas, sealing off the area to prevent the entry of harmful substances, and maintaining communication with emergency personnel.
6. Incident Reporting and Investigation: After an emergency, it is crucial to have procedures in place to report and investigate the incident. This includes establishing protocols for employees to report the details of the emergency, initiating incident investigations to identify the causes and contributing factors, and implementing corrective actions to prevent similar incidents from occurring in the future.
7. Regular Training and Drills: Training and drills are vital for ensuring that employees are prepared to respond effectively during emergencies. Procedures should outline the frequency and types of training sessions and drills conducted, as well as the specific skills and knowledge employees need to develop. This may include fire drills, evacuation drills, or tabletop simulations of various emergency scenarios.
By implementing these emergency response and preparedness procedures, organizations can effectively respond to emergencies, protect employees, and minimize the potential impact of unforeseen events. Regular training, frequent drills, and continuous improvement of emergency response plans are essential for maintaining a state of preparedness and ensuring the safety of all employees.
Employee Training and Communication Procedures
Employee training and communication procedures are essential for creating a culture of safety and ensuring that all employees are equipped with the knowledge and information necessary to work safely. Effective training and communication programs help educate employees about potential hazards, safe work practices, and emergency procedures. Let’s explore the key procedures involved in employee training and communication in more detail.
1. Comprehensive Training Programs: Organizations should develop comprehensive training programs that cover all relevant health and safety topics. These programs should be tailored to the specific job roles and tasks performed by employees. Training can include topics such as hazard identification, proper equipment usage, ergonomics, chemical safety, and emergency response procedures. Regular training sessions should be conducted, both during new employee orientation and as part of ongoing professional development.
2. Clear Communication Channels: Establishing clear communication channels is crucial for effective employee communication. This includes ensuring that all employees are aware of how to report hazards or safety concerns and providing multiple avenues for reporting, such as designated safety emails, suggestion boxes, or anonymous reporting systems. Regular communication updates should be provided to employees to keep them informed about changes in procedures, regulations, or any new hazards identified.
3. Visual Communication: Using visual aids, such as safety posters, signs, and labels, enhances employee awareness and reinforces important safety messages. Visual communication should be clear, concise, and easily understandable. Visual cues can include symbols, color coding, and diagrams, helping to convey safety information quickly and effectively. They can be used to emphasize specific safety procedures, indicate hazardous areas, or remind employees of PPE requirements.
4. Training on Equipment and Tools: Employees should receive thorough training on equipment and tools used in their job roles. This includes proper operation, maintenance, and safety precautions related to the equipment. Organizations should ensure that employees are trained on the safe handling of machinery, power tools, and any specialized equipment. Regular refresher training can help reinforce safe operating procedures and update employees on new equipment or technology.
5. Toolbox Talks or Safety Meetings: Toolbox talks or safety meetings provide valuable opportunities for focused discussions on specific safety topics and allow employees to ask questions or share their experiences. These talks can be delivered in small groups or during team meetings, focusing on particular hazards relevant to the specific work area. It is an effective way to encourage open communication, address concerns, and foster a culture of safety within the organization.
6. Online and E-Learning Platforms: Utilizing online and e-learning platforms can offer flexibility and convenience in delivering training to employees. These platforms provide interactive modules and quizzes that can be completed at employees’ own pace. E-learning platforms can be particularly useful for organizations with remote or geographically dispersed employees, ensuring consistent and accessible training for all.
7. Performance Feedback and Evaluation: Regular feedback and evaluation help measure the effectiveness of training programs and identify areas for improvement. Organizations should establish mechanisms for assessing employees’ understanding and competency in following safety procedures. This may involve quizzes, practical assessments, or observations. Feedback should be provided to individuals or teams to acknowledge their strengths and provide coaching or additional training when needed.
By implementing these employee training and communication procedures, organizations foster a safety-conscious work environment. Proper training and effective communication ensure that employees are knowledgeable about hazards, equipped with the skills to work safely, and empowered to report safety concerns. Regular updates and feedback facilitate ongoing improvement and contribute to a culture where safety is prioritized by all employees.
Procedures for Incident Reporting and Investigation
Incident reporting and investigation procedures are crucial for organizations to promptly address and learn from workplace incidents, accidents, near misses, and occupational illnesses. These procedures provide a systematic approach to gather information, identify root causes, and implement corrective actions. Let’s explore the key procedures involved in incident reporting and investigation in more detail.
1. Clear Reporting Protocols: Establishing clear reporting protocols is essential to encourage employees to promptly report any incidents or potential hazards they observe. Employees should be aware of how and to whom they should report incidents. This can include designated safety officers, supervisors, or a centralized incident reporting system.
2. Timely Reporting: Procedures should emphasize the importance of timely reporting. Encouraging employees to report incidents as soon as possible helps ensure that appropriate actions can be taken promptly, reducing the risk of further injuries, damage, or recurrence of similar incidents.
3. Documenting Information: Procedures should outline the specific information that needs to be documented during incident reporting. This typically includes details about the nature of the incident, date and time, individuals involved, witnesses, location, equipment used, and any contributing factors. Documentation should be factual, objective, and comprehensive.
4. Investigation Team: Designating a team responsible for incident investigations ensures a systematic and thorough examination of incidents. The team can include representatives from various departments or disciplines, such as safety, operations, and human resources. Their role is to collect evidence, analyze facts, and identify root causes.
5. Root Cause Analysis: Conducting a root cause analysis is crucial in understanding the underlying factors that contributed to the incident. Procedures should outline methodologies for determining the root causes, such as using techniques like the “Five Whys” or the “Fishbone Diagram.” The goal is to identify not only the immediate causes but also any underlying systemic issues or process deficiencies.
6. Corrective Actions: Once the root causes are identified, it is essential to develop and implement corrective actions to prevent similar incidents in the future. Procedures should outline the process for developing these actions, including assigning responsibilities, setting deadlines, and regularly monitoring progress. Corrective actions may involve changes in procedures, additional training, equipment modifications, or policy updates.
7. Communication: Clear and effective communication is essential during incident reporting and investigation procedures. Communication protocols should outline how incident information will be shared with relevant stakeholders, such as managers, supervisors, and employees. Timely and transparent communication fosters trust, demonstrates the organization’s commitment to safety, and ensures that valuable lessons learned can be shared across the organization.
8. Confidentiality: Procedures should reinforce the importance of maintaining confidentiality during incident reporting and investigation. Employees should feel assured that their involvement in reporting incidents or providing witness statements will be treated confidentially, reducing any potential fear of retaliation and encouraging open reporting.
9. Continuous Improvement: Procedures for incident reporting and investigation should be periodically reviewed and updated to ensure their effectiveness. Regular evaluation of the procedures, including feedback from employees and key stakeholders, can help identify areas for improvement and enhancements.
By implementing these incident reporting and investigation procedures, organizations can effectively address incidents and prevent their recurrence. Timely reporting, comprehensive investigations, effective root cause analysis, and corrective actions contribute to a safer work environment and help build a proactive safety culture where incidents are viewed as opportunities for learning and improvement.
Auditing and Evaluation Procedures
Auditing and evaluation procedures play a vital role in maintaining an effective health and safety program. These procedures help organizations assess the implementation and effectiveness of safety measures, identify areas for improvement, and ensure ongoing compliance with regulations. Let’s explore the key procedures involved in auditing and evaluating health and safety programs in more detail.
1. Internal Audits: Internal audits are critical in assessing the overall effectiveness of the health and safety program. Procedures should outline the frequency and scope of internal audits, which may be conducted by an internal safety team or an external consultant. Audits help organizations identify gaps in compliance, areas of improvement, and any potential deficiencies in safety procedures or control measures.
2. Audit Checklists and Tools: Audit checklists and tools can be valuable in ensuring consistency and thoroughness during the auditing process. These documents outline specific areas and criteria to be evaluated, such as hazard identification, training records, maintenance logs, and emergency response plans. Procedures should specify the use of such tools to ensure a comprehensive evaluation of the health and safety program.
3. Compliance Evaluation: Compliance with laws, regulations, and industry standards is a crucial aspect of auditing and evaluation procedures. Procedures should specify the requirements to be assessed, such as the Occupational Safety and Health Administration (OSHA) standards and any specific regulations applicable to the organization’s industry. Evaluating compliance helps identify any gaps and address areas of non-compliance.
4. Key Performance Indicators (KPIs): Establishing and tracking key performance indicators are important in evaluating the effectiveness of the health and safety program. Procedures should define relevant KPIs, such as the number of incidents, lost-time injury rates, near-miss reporting, training completion rates, and compliance with safety protocols. Monitoring KPIs enables organizations to measure progress, identify trends, and make informed decisions based on data-driven insights.
5. Safety Culture Assessment: Procedures should include methods for assessing the safety culture within the organization. This can be done through employee surveys, interviews, or focus groups to gather feedback regarding perceptions of safety, communication, involvement, and management commitment. Assessing the safety culture helps identify areas where improvements can be made to develop a culture of safety at all levels of the organization.
6. Management Review: Regular management reviews are essential in evaluating the overall effectiveness of the health and safety program. This involves reviewing audit findings, KPIs, incident reports, and other relevant data to assess the program’s performance. Procedures should outline the frequency and format of management reviews, ensuring that they are conducted at appropriate intervals and involve key decision-makers.
7. Continuous Improvement: Procedures for auditing and evaluation should emphasize the importance of continuous improvement. Organizations should establish processes for capturing lessons learned from audits, incidents, and evaluations. These lessons should then be used to drive improvements in processes, procedures, training, and control measures. By continuously refining the health and safety program, organizations can strive for ongoing improvement and enhance overall safety performance.
8. Corrective and Preventive Actions: Auditing and evaluation procedures should include specific steps for implementing corrective and preventive actions based on audit findings and evaluations. Procedures should outline the process for assigning responsibilities, setting timelines for completion, and monitoring the progress of these actions. By addressing identified gaps and deficiencies, organizations can mitigate risks, improve safety performance, and prevent recurrent incidents.
By following these auditing and evaluation procedures, organizations can ensure the effectiveness of their health and safety programs. Regular audits, compliance evaluations, safety culture assessments, and continuous improvement efforts contribute to creating a safe and healthy work environment, fostering employee well-being, and minimizing potential risks.
Conclusion
Creating a safe and healthy work environment is of utmost importance for organizations in all industries. The implementation of robust health and safety procedures and programs is crucial in achieving this goal. From the Occupational Safety and Health Act (OSH Act) to federal regulations and standards, organizations have a legal and moral obligation to protect their employees from potential hazards.
The Health and Safety Program Document serves as a comprehensive guide for employees and management to understand and follow specific procedures and programs. It outlines the steps for identifying, assessing, controlling, and managing hazards in the workplace. By having a well-documented program, organizations can foster a culture of safety and ensure compliance with regulations, enhancing the well-being of their employees.
The importance of health and safety procedures cannot be overstated. They not only promote employee safety, but they also contribute to increased productivity, reduced costs, and improved reputation. Organizations that prioritize health and safety demonstrate a commitment to their employees and are more likely to attract and retain top talent.
Key elements of a comprehensive health and safety program include procedures for hazard identification and assessment, hazard control and management, emergency response and preparedness, employee training and communication, incident reporting and investigation, as well as auditing and evaluation procedures. Each of these elements plays a crucial role in promoting a safe and healthy work environment.
By effectively implementing procedures for identifying and assessing hazards, organizations can proactively identify potential risks and take appropriate measures to control and manage them. Similarly, procedures for controlling and managing hazards, including engineering controls, administrative controls, and the proper use of personal protective equipment, are essential in minimizing risks and preventing accidents.
Emergency response and preparedness procedures ensure that organizations are equipped to address unexpected events and safeguard the well-being of their employees. Employee training and communication procedures foster a safety-conscious culture, where employees understand potential hazards, receive proper training, and actively participate in safety initiatives.
Incident reporting and investigation procedures enable organizations to learn from incidents, identify root causes, and implement corrective actions to prevent future occurrences. Auditing and evaluation procedures provide organizations with the means to assess the effectiveness of their health and safety programs, identify areas for improvement, and ensure compliance with regulations.
In conclusion, organizations must prioritize the implementation of comprehensive health and safety procedures and programs. By doing so, they not only fulfill their legal obligations, but they also protect their most valuable asset—their employees. A strong commitment to workplace safety contributes to a culture of well-being, productivity, and positive reputation. Regular evaluation, continuous improvement, and a proactive approach to health and safety create a work environment where employees feel safe and supported, allowing them to thrive and contribute to the overall success of the organization.