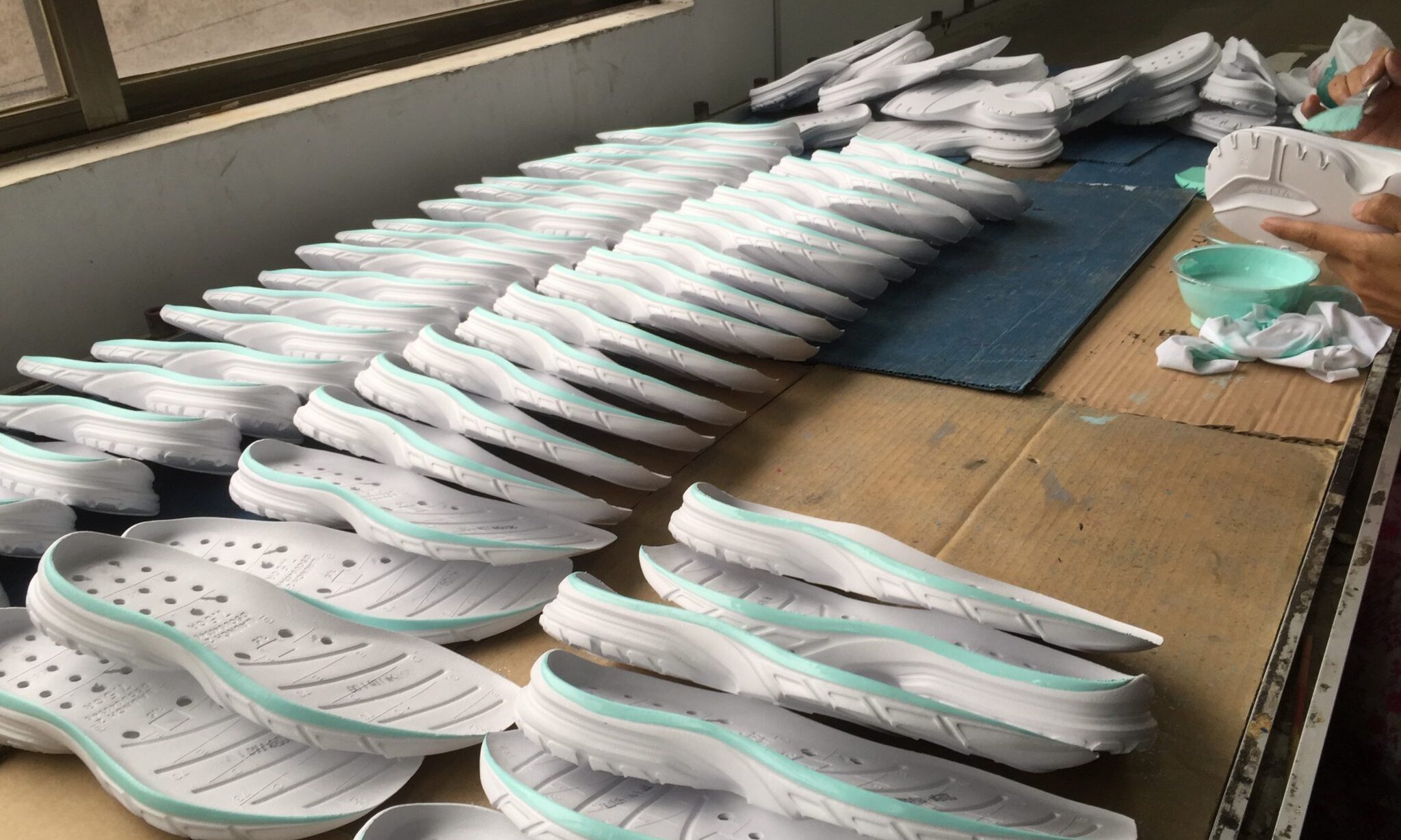
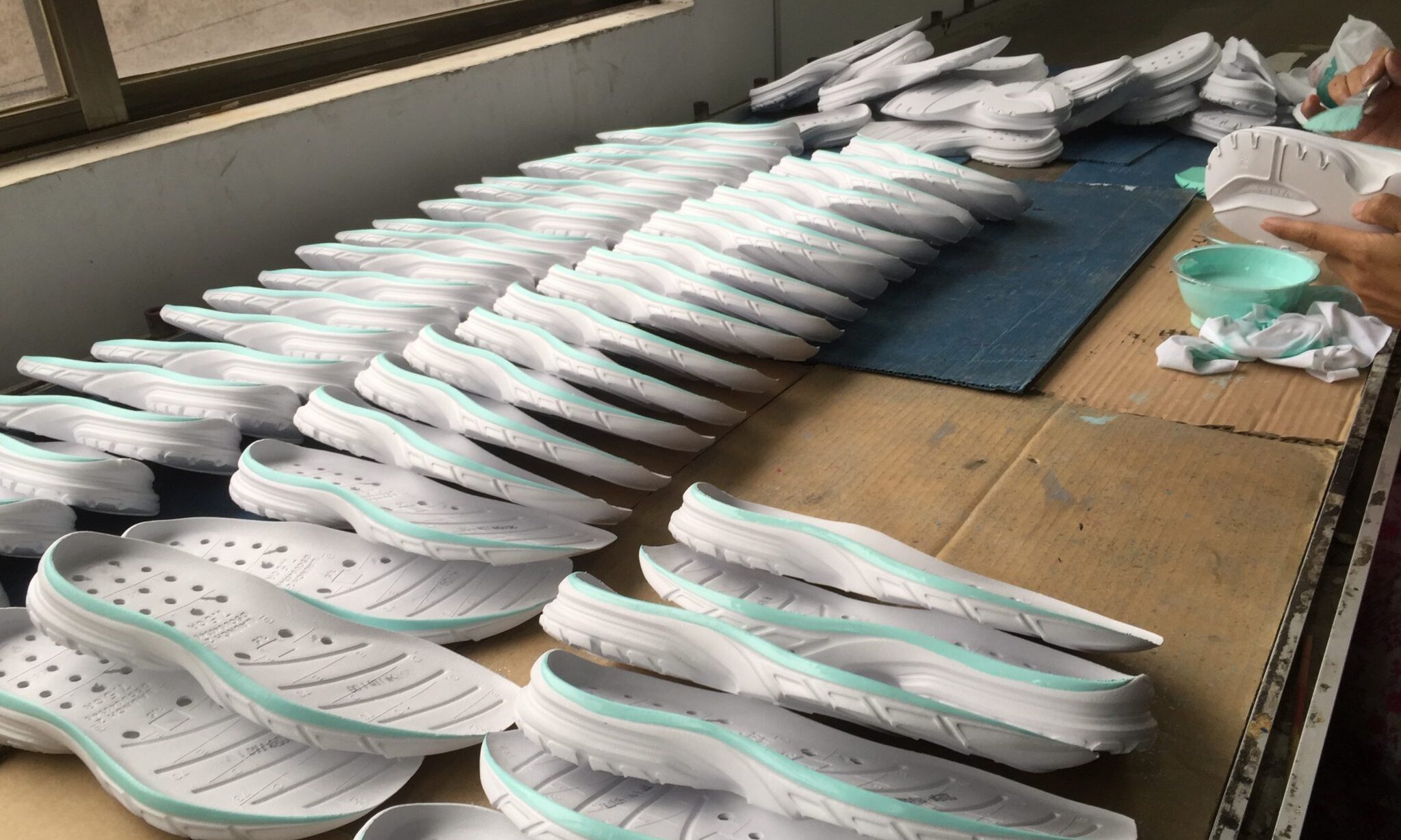
Featured
How Running Shoes Are Made
Modified: May 22, 2024
Discover the process behind how running shoes are made, featuring insights on materials, design, and manufacturing techniques. Explore the journey from concept to creation.
Introduction
Welcome to the world of running shoes, where technology and craftsmanship merge to create the perfect footwear for athletes and enthusiasts alike. Running shoes are more than just fashionable accessories – they are meticulously designed to provide support, cushioning, and stability for runners of all levels. Understanding how running shoes are made can give you a deeper appreciation for the engineering and innovation behind these essential pieces of athletic equipment.
Whether you are a casual jogger or a seasoned marathon runner, choosing the right running shoes is crucial to optimizing your performance and reducing the risk of injury. The manufacturing process involves a combination of advanced materials, cutting-edge technologies, and skilled craftsmanship, all aimed at creating running shoes that deliver optimal comfort, durability, and performance.
In this article, we will take a closer look at the materials used, construction techniques, and quality control measures that go into making running shoes. By gaining insight into this fascinating process, you will be better equipped to make informed choices when it comes to purchasing your next pair of running shoes.
Materials Used in Running Shoe Manufacturing
Running shoes are made using a combination of synthetic and natural materials, each chosen for its specific functional properties. These materials are carefully selected to provide durability, flexibility, breathability, and support.
The upper part of the shoe, which covers the foot, is usually made from a combination of mesh, synthetic fabrics, and leather. Mesh is used for its lightweight and breathable properties that allow air to flow freely and keep the feet cool and dry during physical activity. Synthetic fabrics provide durability and support, while leather is often used for its stylish appearance and added durability.
The midsole, located between the upper and the outsole, is where the majority of the shoe’s cushioning and support is found. Most midsoles are made from ethylene-vinyl acetate (EVA) foam, a lightweight and highly shock-absorbent material. This foam helps to absorb impact and reduce stress on the joints, providing a comfortable and responsive feel while running. Some running shoes also incorporate thermoplastic polyurethane (TPU) or thermoplastic elastomer (TPE) in the midsole to enhance stability and responsiveness.
The outsole, designed to provide traction and protect the shoe from wear and tear, is typically made of rubber or a rubber compound. It features a pattern of treads and grooves that enhance grip and provide traction on various surfaces. The type of rubber used can vary depending on the intended use of the shoe – some are softer for better grip on pavement, while others are harder for increased durability on rough terrain.
In addition to these primary materials, running shoes often incorporate various other components that contribute to their functionality. These include foam insoles for additional cushioning and arch support, heel counters for stability and control, and padding and reinforcements in specific areas of the shoe to provide extra protection and support.
By carefully selecting and combining these materials, running shoe manufacturers are able to create footwear that offers a balance of comfort, durability, and performance. The choice of materials plays a significant role in determining the overall functionality and performance of the shoe, making it essential for manufacturers and consumers alike to stay informed about the latest advancements in material technology.
Upper Construction
The upper construction of a running shoe refers to the part of the shoe that wraps around and provides support to the foot. It is responsible for securing the foot in place and protecting it from external elements.
The upper is typically made of several layers of materials, including mesh, synthetic fabrics, and sometimes leather. These materials are strategically combined to provide a balance of breathability, flexibility, and structural integrity.
The first layer, often made of mesh, is lightweight and breathable. It allows air to circulate inside the shoe, preventing excessive heat and moisture buildup and keeping the feet cool and dry during long runs. The mesh is typically tightly-knit to provide adequate support and prevent debris from entering the shoe.
Underneath the mesh layer, there are additional layers of synthetic fabrics and structural reinforcements. These layers are responsible for providing stability and support to the foot, especially around the midfoot and heel areas. They help to prevent excessive foot movement, reduce the risk of injuries, and enhance overall performance.
In some running shoe models, leather is used in the upper construction to provide added durability and a stylish aesthetic. Leather panels are strategically placed in areas prone to wear and tear, such as the toe cap and heel, to enhance the shoe’s longevity and protect against abrasion.
Additionally, the upper construction incorporates various design elements and features to enhance the shoe’s fit and performance. This includes lacing systems, such as traditional laces or quick-lace systems, that allow wearers to customize the fit and snugness of the shoe. Some running shoes also feature overlays or support structures that provide extra stability and structure to specific areas of the foot, such as the arch or heel.
The upper construction is a critical component of a running shoe, as it directly impacts the fit, comfort, and performance of the shoe. Manufacturers carefully design and engineer the upper to ensure that it provides optimal support, flexibility, and breathability. By understanding the different materials and design features found in the upper construction, runners can select the right shoe that suits their specific running needs and preferences.
Midsole Construction
The midsole is a crucial part of a running shoe, responsible for providing cushioning, support, and stability to the foot. It is situated between the upper and the outsole, acting as a shock absorber to attenuate the impact forces experienced during running.
The primary material used in midsole construction is ethylene-vinyl acetate (EVA) foam. This foam is known for its lightweight and responsive properties. It effectively absorbs and disperses the impact forces generated with each step, reducing stress on the joints and preventing injuries. The density and thickness of the EVA foam can vary depending on the intended purpose of the shoe, with some shoes having softer midsoles for enhanced cushioning and others having firmer midsoles for better stability and energy return.
In addition to EVA foam, some running shoe manufacturers incorporate other materials and technologies into the midsole to offer improved performance and support. For example, thermoplastic polyurethane (TPU) or thermoplastic elastomer (TPE) compounds may be used to provide stability and responsiveness. These materials help to control excessive foot pronation and enhance the shoe’s ability to return energy to the wearer during each stride.
Midsoles are often designed with specific cushioning technologies, such as air or gel pockets, to further enhance shock absorption and provide a more comfortable running experience. These technologies help to distribute the forces evenly and reduce impact on the foot and lower body, promoting a smoother gait cycle.
Running shoe manufacturers also employ various midsole construction techniques to optimize performance and comfort. Some shoes feature a dual-density midsole, where different areas of the midsole have varying levels of firmness to provide targeted support and cushioning. Others may use compression molding or injection molding processes to create a precisely contoured midsole that cradles the foot and enhances stability.
While the midsole is an essential component of a running shoe, it is important to note that its materials and construction can affect the shoe’s lifespan. The midsole can gradually lose its cushioning properties over time, leading to a less supportive and comfortable shoe. Therefore, it is recommended to replace running shoes after a certain mileage or when signs of wear and tear become apparent.
Understanding the construction and materials used in the midsole allows runners to choose shoes that suit their specific performance and comfort needs. By considering factors such as cushioning, stability, and responsiveness, individuals can find the perfect pair of running shoes that enhances their running experience and minimizes the risk of injury.
Outsole Construction
The outsole of a running shoe is the part that comes into direct contact with the ground. It plays a critical role in providing traction, durability, and protection to the foot during the running motion.
Outsoles are typically made of rubber or rubber compounds due to their excellent grip and flexibility. The type of rubber used can vary depending on the specific needs of the shoe. Some outsoles are engineered with softer rubber to provide better grip on smooth surfaces like pavement, while others use harder rubber for increased durability on rough trails.
The outsole is designed with patterns of treads and grooves to enhance traction and provide stability on various surfaces. These patterns help to channel water away and prevent slippage on wet terrain, making them suitable for running in different weather conditions. The depth and pattern of the treads can vary depending on the intended use of the shoe – trail running shoes, for example, often have more aggressive lugs for better grip on uneven and slippery surfaces.
In addition to the rubber material and tread pattern, running shoe outsoles may also incorporate technologies aimed at enhancing performance. Some shoes utilize carbon rubber or blown rubber in specific areas of the outsole to provide better durability and reduce weight. These materials maintain grip and protect against wear in high-impact zones.
Outsole construction also includes flex grooves strategically placed to promote natural foot movement and flexibility. These grooves allow the foot to flex and bend in the correct points during the running motion, promoting a more efficient stride and reducing the risk of injuries.
Manufacturers often conduct extensive testing to ensure the durability and functionality of the outsole. Abrasion testing, for example, is performed to assess the outsole’s resistance to wear and tear. This testing helps manufacturers determine the ideal rubber compound and tread pattern for specific running conditions.
It’s important to note that the lifespan of the outsole will depend on factors such as the type of terrain on which the shoes are used and the mileage accumulated. As the outsole wears down, the tread depth decreases, reducing traction and increasing the risk of slipping.
By understanding the construction of the outsole and the materials used, runners can choose shoes that offer the right traction, durability, and protection for their specific running needs. Selecting the appropriate outsole design for the running surface and considering factors such as tread pattern and rubber compound can greatly enhance the overall performance and safety of a running shoe.
Additional Features and Technologies
In addition to the primary construction components, modern running shoes often incorporate a range of additional features and technologies that aim to enhance performance, comfort, and injury prevention.
One popular technology found in many running shoes is the presence of cushioning systems. These systems, such as Nike’s Air cushioning or adidas’ Boost foam, provide enhanced shock absorption and energy return. They help to reduce the impact on joints and muscles during each stride, making the running experience more comfortable and efficient.
Another common feature is the inclusion of stability mechanisms to assist with proper foot alignment. Many running shoes have medial posts or dual-density midsoles that offer added support to prevent excessive inward rolling of the foot, known as overpronation. Likewise, some shoes have lateral designs that provide extra stability for runners with supination, where the foot rolls outward.
Running shoes also incorporate technologies to improve breathability, such as mesh uppers with enhanced ventilation or moisture-wicking lining materials. These features help to regulate the temperature and moisture inside the shoe, keeping the foot cool and dry even during intense workouts.
Some manufacturers utilize lightweight and durable materials, like carbon fiber or TPU (thermoplastic polyurethane), in specific areas of the shoe to reinforce structural integrity and minimize weight. These technologies enhance performance by providing a balance between stability and responsiveness without compromising on durability or support.
Various lacing systems are also employed to optimize the fit and customize the snugness of the shoe. Lace designs, such as traditional laces or quick-lace systems, allow for easy adjustments and secure foot lockdown. This ensures a personalized fit that can enhance comfort and prevent the foot from sliding inside the shoe during runs.
Many running shoe models incorporate reflective materials on the upper or outsole to increase visibility during low-light conditions. These reflective elements improve safety by making the runner more visible to pedestrians, cyclists, and drivers.
Additional features to enhance the running experience include cushioned or contoured insoles, anti-microbial treatments to reduce odor, and padded collars and tongues for extra comfort and protection. Some shoes even offer removable sock liners, making it easy to replace or customize with orthotics if needed.
The incorporation of these features and technologies is the result of continuous innovation and research by running shoe manufacturers. They strive to provide runners with footwear that is not only comfortable and durable but also aids in performance, injury prevention, and overall wellbeing.
When selecting a pair of running shoes, it is essential to consider these additional features and technologies to find the perfect fit for your specific needs and preferences. Whether you are a casual runner or a competitive athlete, choosing a shoe that incorporates the right combination of features can significantly enhance your running experience.
Quality Control in Running Shoe Manufacturing
Quality control is a critical aspect of the manufacturing process for running shoes. Without stringent quality control measures in place, the consistency, performance, and durability of the final product could be compromised. Therefore, running shoe manufacturers implement various quality control procedures to ensure that every pair of shoes meets and exceeds industry standards.
One of the essential aspects of quality control is material inspection. Manufacturers carefully check all incoming materials, such as fabrics, foams, and rubber compounds, to ensure they meet the required specifications. This ensures that only high-quality materials are used in the production of running shoes, which ultimately enhances their performance and longevity.
During the production process, quality control teams conduct regular inspections at various stages. They check for any manufacturing defects, such as improper stitching, misaligned components, or issues with bonding and adhesion. These inspections help identify and rectify any issues early on, preventing defective products from reaching the market.
Another key quality control measure is performance testing. Running shoe manufacturers subject their products to a battery of tests to ensure they meet the expected performance standards. This includes testing for cushioning properties, flexibility, stability, and traction. Shoes may also undergo specialized tests to evaluate water resistance, durability, and impact absorption.
Fit and comfort are vital aspects of running shoes, and quality control teams pay close attention to these factors. Fit tests are conducted to assess the shoe’s overall fit and determine if any adjustments are necessary. The comfort level of the shoe, including factors such as padding, arch support, and collar and tongue design, is also carefully evaluated.
Manufacturers also carry out wear testing, where prototypes or samples are given to runners to test in real-world conditions. Feedback from these wear testers is invaluable as it helps identify any areas for improvement and ensures that the shoes meet the needs of runners across a range of terrains and distances.
In addition to in-house quality control measures, many reputable running shoe manufacturers adhere to industry standards and certifications. These standards, such as ISO 9001, ensure that a set of quality management processes are followed during the manufacturing process. This further guarantees that the shoes meet the required quality benchmarks.
By implementing strict quality control measures, running shoe manufacturers strive to deliver consistent and high-performance products to consumers. These measures not only help maintain the reputation of the brand but also enable customers to trust that the shoes they are buying are of the highest quality and will meet their athletic needs.
When purchasing running shoes, it is beneficial to seek out brands that have a reputation for rigorous quality control. This ensures that you are investing in a reliable and durable pair of shoes that will support your running activities and withstand the rigors of training and competition.
Conclusion
Understanding how running shoes are made offers invaluable insight into the craftsmanship, innovation, and technology that goes into creating these essential athletic footwear. The materials used, the construction techniques employed, and the quality control measures implemented by manufacturers all contribute to producing running shoes that provide optimal support, comfort, and performance.
The materials used in running shoe manufacturing, such as mesh, synthetic fabrics, EVA foam, and rubber, are carefully selected to offer a balance of breathability, flexibility, cushioning, and durability. These materials, combined with advanced construction techniques, result in shoes that can handle the demands of various terrains and provide the necessary support for runners of all levels.
Additional features and technologies found in running shoes enhance performance, comfort, and injury prevention. These include cushioning systems, stability mechanisms, breathable designs, traction-enhancing outsole patterns, and various lacing systems. These elements are continually evolving as manufacturers strive to deliver running shoes that meet the specific needs and preferences of athletes and enthusiasts.
Throughout the manufacturing process, quality control plays a vital role in ensuring that every pair of running shoes meets industry standards for performance, durability, and comfort. Extensive testing, both in the lab and through wear testing, helps to identify and rectify any issues early on, ensuring that only high-quality products reach the market.
As runners, it is important to consider the various factors involved in the production of running shoes. By understanding the materials used, the construction techniques employed, and the quality control measures implemented, we can make informed decisions when choosing the right pair of running shoes for our individual needs and preferences.
So the next time you slip on your running shoes, take a moment to appreciate the craftsmanship and technology that have gone into creating that perfect blend of comfort, performance, and style. Whether you’re embarking on a casual jog or pushing your limits in a marathon, your running shoes are there to support you every step of the way.