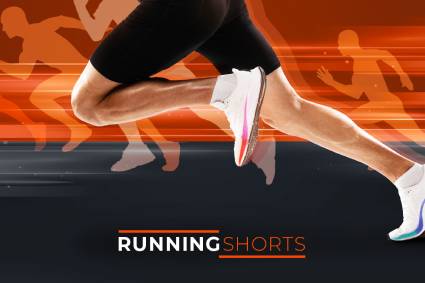
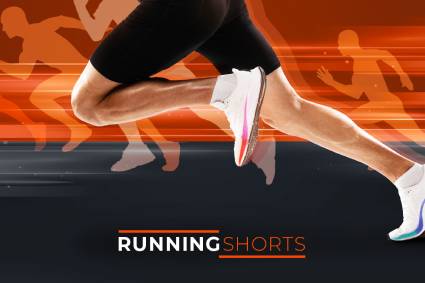
Featured
What Is The Endurance Limit
Published: August 12, 2023
Discover the featured topic of "What Is The Endurance Limit" and explore its significance in withstanding fatigue and durability, explained by experts.
Introduction
Welcome to the world of engineering and materials science, where strength and durability are of utmost importance. In this article, we will explore a critical concept known as the endurance limit. The endurance limit plays a crucial role in determining the structural integrity and longevity of various engineering components.
When it comes to designing and manufacturing mechanical systems, it is essential to understand how materials respond to cyclic loads. Cyclic loading refers to repeated applications of stress, which can cause fatigue and ultimately lead to failure. However, materials have their limits, and beyond a certain point, fatigue failure can occur even at relatively low stress levels. This is where the concept of endurance limit comes into play.
The endurance limit, also known as the fatigue strength or fatigue limit, is defined as the maximum stress level a material can withstand indefinitely without experiencing fatigue failure. It represents the stress threshold below which a material can tolerate cyclic loading for an infinite number of cycles. Understanding and accurately determining the endurance limit is crucial for ensuring the reliability and safety of structural components subjected to repetitive stress.
The endurance limit is particularly important in applications where cyclic loading is common, such as in the aerospace, automotive, and manufacturing industries. By designing components that operate below the endurance limit, engineers can extend the lifespan and improve the performance of various systems. This not only reduces the risk of catastrophic failures but also minimizes maintenance costs and improves overall efficiency.
Multiple factors influence the endurance limit of a material, including its composition, microstructure, and surface condition. The design and manufacturing processes also play a significant role in determining the endurance limit. Therefore, it is essential to thoroughly study and test materials to assess their fatigue behavior and establish accurate endurance limit values.
Throughout this article, we will delve into the factors affecting the endurance limit, explore various testing methodologies used to determine it, and discuss the applications in which the knowledge of endurance limit is vital. So, let’s dive in and unlock the fascinating world of the endurance limit!
Definition of Endurance Limit
The endurance limit, also known as the fatigue strength or fatigue limit, is a fundamental concept in materials science and engineering. It refers to the maximum stress level that a material can withstand indefinitely without experiencing fatigue failure. In other words, it is the threshold below which a material can tolerate cyclic loading without undergoing fatigue-induced damage.
When a material is subjected to cyclic loading, such as repeated stress or strain, microscopic cracks may initiate and propagate. These cracks can eventually lead to failure, even when the applied stress is below the material’s ultimate tensile strength. However, below a certain stress level, known as the endurance limit, the material can withstand cyclic loading for an infinite number of cycles without initiating cracks or experiencing fatigue failure.
The endurance limit is typically determined through fatigue testing, which involves subjecting a test specimen to repeated cyclic loading until failure occurs. The stress levels applied during the testing process are gradually increased until a fatigue failure is observed at a certain stress level. The highest stress level at which the material does not fail after a specified number of cycles is considered to be the endurance limit.
It’s important to note that the endurance limit is specific to each material and can vary significantly. Different materials, such as metals, alloys, and polymers, have different endurance limit values due to variations in their structural properties. For example, steel tends to have a well-pronounced endurance limit, while aluminum alloys exhibit a decreasing endurance limit with increasing stress levels.
The endurance limit is often expressed as a stress value or as a percentage of the material’s ultimate tensile strength (UTS). For instance, if a material has an endurance limit of 50 MPa and a UTS of 100 MPa, it means that the material can withstand cyclic loading indefinitely as long as the applied stress remains below 50 MPa, even though its UTS is higher.
By understanding and utilizing the concept of the endurance limit, engineers can design and manufacture components that operate within safe stress limits, reducing the risk of fatigue failure. This knowledge is crucial in industries where cyclic loading is prevalent, such as aerospace, automotive, and manufacturing. By incorporating the endurance limit into the design process, engineers can optimize the performance, reliability, and longevity of various mechanical systems.
Importance of Endurance Limit
The endurance limit holds immense significance in the field of engineering and materials science. Understanding and considering the endurance limit during the design and manufacturing processes of mechanical components is essential for several reasons.
First and foremost, the endurance limit serves as a fundamental parameter for evaluating the fatigue resistance of materials. It provides critical information on the maximum stress level that a material can endure without experiencing fatigue failure. By designing components that operate below the endurance limit, engineers can ensure their longevity and prevent premature failure due to cyclic loading.
Consequently, considering the endurance limit in the design phase helps improve safety. Components that experience frequent and fluctuating loads, such as aircraft wings, automotive suspension systems, and industrial machinery, must be designed to withstand these cyclic stress conditions. By ensuring that the applied stresses remain below the endurance limit, the risk of catastrophic failures and associated safety hazards is significantly reduced.
In addition to safety, incorporating the endurance limit into the design process also leads to cost savings. Fatigue failures can be time-consuming and expensive to repair or replace. By designing components with knowledge of their endurance limits, engineers can optimize their lifespan and minimize maintenance and replacement costs.
Furthermore, the endurance limit plays a crucial role in improving the performance and efficiency of mechanical systems. By operating components below their endurance limits, engineers can reduce the occurrence of fatigue-related issues, such as crack propagation and material degradation. This, in turn, leads to increased system reliability, improved productivity, and enhanced overall efficiency.
Industries that heavily rely on components subjected to cyclic loading, such as aerospace, automotive, and manufacturing, greatly benefit from knowledge of the endurance limit. Aircraft structures, for example, experience numerous cycles of loading during takeoff, landing, and flight. By considering the endurance limit, engineers can ensure the fatigue resistance of critical components, resulting in safer and more reliable aircraft.
Overall, the endurance limit is a vital parameter in the design and manufacturing of mechanical components. Its importance lies in improving safety, reducing costs, and enhancing system performance. By understanding and incorporating the concept of endurance limit, engineers can create robust and durable systems that can withstand cyclic loading and provide long-lasting performance in a wide range of applications.
Factors Affecting Endurance Limit
The endurance limit of a material is influenced by various factors that determine its ability to withstand cyclic loading without experiencing fatigue failure. Understanding these factors is crucial for accurately predicting and designing components that operate within safe stress limits. Let’s explore some of the key factors that affect the endurance limit.
1. Composition: The chemical composition of a material has a significant impact on its endurance limit. Elements such as carbon, nitrogen, and alloying elements can alter the material’s microstructure and mechanical properties, thereby influencing its fatigue resistance. For example, high carbon content in steel can increase its strength but decrease its endurance limit.
2. Microstructure: The arrangement and distribution of grains, phase constituents, and internal imperfections within a material’s microstructure influence its endurance limit. Fine-grained materials generally exhibit higher endurance limits compared to coarse-grained materials, as they have improved resistance to crack initiation and propagation.
3. Surface Condition: Surface imperfections, such as scratches, notches, and residual stresses, can act as stress concentration points and significantly reduce the endurance limit of a material. Proper surface treatment and finishing processes are necessary to minimize these imperfections and enhance the fatigue resistance.
4. Temperature: Elevated temperatures can significantly affect the endurance limit of materials. High temperatures can promote creep deformation and reduce material strength, leading to a decrease in the endurance limit. Thermal cycling can also induce fatigue failure at lower stress levels.
5. Loading Frequency: The frequency at which cyclic loading is applied to a material can affect its endurance limit. Higher loading frequencies often result in lower endurance limits due to reduced time for stress relaxation and increased heat generation, leading to accelerated fatigue damage.
6. Notch Sensitivity: Materials with high notch sensitivity, such as certain alloys and brittle materials, tend to have lower endurance limits. Notches act as stress concentration points, amplifying the applied stress and promoting crack initiation and propagation.
7. Environmental Factors: Environmental conditions, such as humidity, temperature variations, and corrosive media, can significantly influence a material’s endurance limit. Corrosion, for instance, can decrease the endurance limit by promoting crack initiation and accelerating fatigue damage progression.
It is important to note that these factors do not act independently but often interact with each other in a complex manner. Therefore, understanding the combined effect of these factors is crucial for accurately predicting and optimizing the endurance limit of a material.
By considering these factors and conducting thorough testing and analysis, engineers can design components that operate within safe stress limits and have improved fatigue resistance. This knowledge allows for the development of materials and structural designs that can withstand cyclic loading and ensure long-term durability and reliability.
Testing Methodologies for Endurance Limit
Accurately determining the endurance limit of a material is crucial for designing components that operate within safe stress limits. Various testing methodologies have been developed to assess the fatigue resistance and establish the endurance limit. Let’s explore some of the commonly used testing methods:
1. S-N Curve Testing: The S-N curve, also known as the stress-life curve, is a widely used method for determining the endurance limit. In this test, a series of specimens of the material are subjected to cyclic loading at different stress levels. The number of cycles to failure is recorded, and the obtained data is plotted on a graph to create the S-N curve. The endurance limit is then determined as the stress level at which a specified number of cycles, often several million cycles, can be sustained without failure.
2. Step-Stress Testing: This testing method involves gradually increasing the stress levels applied to the specimen in a stepwise manner. The stress is increased incrementally until failure occurs. This method allows for the determination of the endurance limit by identifying the maximum stress level at which the material can sustain a specified number of cycles without failure.
3. Variable-Amplitude Testing: Unlike constant-amplitude testing, variable-amplitude testing involves subjecting the specimen to varying stress levels that simulate real-world operating conditions. This method is useful for determining the endurance limit under realistic loading conditions, where the applied stress levels fluctuate throughout the component’s service life.
4. Resonance Testing: Resonance testing is particularly useful for assessing the fatigue behavior of brittle materials or components with complex geometries. The specimen is subjected to cyclic loading at its natural frequency, which amplifies the stresses and accelerates fatigue damage. This allows for the determination of the endurance limit under worst-case scenarios.
5. Finite Element Analysis (FEA): Finite Element Analysis is a numerical simulation technique used to predict the endurance limit of components based on their geometry, material properties, and loading conditions. FEA helps identify stress concentrations, evaluate the effects of different design and material parameters, and optimize the component’s fatigue resistance.
6. Probabilistic Testing: Probabilistic testing methods, such as the staircase method or the up-and-down method, involve testing a group of specimens at gradually increasing or decreasing stress levels. By analyzing the statistical variations in the results, the endurance limit can be estimated with a certain degree of confidence.
It is important to mention that testing for the endurance limit should be performed under controlled conditions and in accordance with standardized testing procedures. Factors such as specimen preparation, sample size, testing frequency, and environmental conditions must be carefully controlled to ensure reliable and accurate results.
By employing these testing methodologies, engineers can gain valuable insights into the fatigue behavior of materials and establish the endurance limit. This knowledge guides the design of components that can withstand cyclic loading and ensures the reliability, durability, and safety of various engineering systems.
Applications of Endurance Limit
The concept of endurance limit plays a crucial role in numerous industries where components are subjected to cyclic loading. Understanding and utilizing the endurance limit is vital for designing and manufacturing mechanical systems that can withstand long-term stress conditions. Let’s explore some of the key applications of the endurance limit:
1. Aerospace Industry: The aerospace industry heavily relies on components that experience cyclic loading during various stages of flight, such as takeoff, landing, and turbulence. Understanding the endurance limit is crucial for designing and manufacturing aircraft structures, engine components, and landing gears that can withstand these cyclic stress conditions and ensure safe and reliable operation.
2. Automotive Industry: In the automotive industry, components such as engine parts, suspension systems, and drivetrain components are subjected to repeated stress and strain during vehicle operation. By considering the endurance limit, engineers can design durable and fatigue-resistant components that can withstand the demanding conditions of everyday driving.
3. Manufacturing Industry: The manufacturing industry encompasses a wide range of applications, from heavy machinery to consumer goods production. Understanding the endurance limit is essential for the design and fabrication of equipment and machinery that undergo cyclic loading, such as presses, turbines, and conveyors. By optimizing the endurance limit, manufacturers can increase productivity, minimize downtime, and improve overall operational efficiency.
4. Medical Implants: Implants used in medical applications, such as hip and knee replacements, must endure cyclic loading due to the normal movement and demands placed on the human body. Understanding the endurance limit is vital for designing implants that can withstand repetitive stress over extended periods without failure, ensuring the long-term success of the implant and the well-being of the patients.
5. Civil Engineering: In civil engineering, structures such as bridges, buildings, and dams are subjected to various loading conditions, including wind, seismic activity, and traffic vibrations. Knowledge of the endurance limit enables engineers to design and construct structures that can withstand these cyclic loading scenarios, ensuring the safety and longevity of the infrastructure.
6. Power Generation: Power generation facilities, including turbines, generators, and wind turbines, often experience cyclic loading due to rotational forces and fluctuating energy demands. Understanding the endurance limit is crucial for designing and maintaining these components to withstand the cyclic stressors and ensure uninterrupted power supply.
These are just a few examples of the many applications where knowledge of the endurance limit is essential. By incorporating the endurance limit into the design and manufacturing processes, engineers can optimize the fatigue resistance of components, enhance reliability and safety, prolong the lifespan of systems, and ultimately contribute to overall efficiency and sustainability in various industries.
Conclusion
The concept of endurance limit is vital in the field of engineering and materials science, as it determines the maximum stress level that a material can endure indefinitely without experiencing fatigue failure. By understanding and considering the endurance limit during the design and manufacturing processes, engineers can ensure the reliability, safety, and longevity of mechanical components exposed to cyclic loading.
Throughout this article, we have explored the definition and importance of the endurance limit. We have learned that the endurance limit represents the stress threshold below which a material can tolerate cyclic loading for an infinite number of cycles. Components designed to operate below this limit can resist fatigue-induced damage and offer improved performance, reduced maintenance costs, and enhanced efficiency. We have also examined the factors that affect the endurance limit, including composition, microstructure, surface condition, temperature, loading frequency, notch sensitivity, and environmental factors.
Moreover, we have discussed various testing methodologies used to determine the endurance limit, such as S-N curve testing, step-stress testing, variable-amplitude testing, resonance testing, finite element analysis, and probabilistic testing. These testing methods allow engineers to accurately assess the fatigue resistance and establish the endurance limit of materials, enabling the design of components that can withstand cyclic loading under specific operating conditions.
Lastly, we have explored the wide range of applications where knowledge of the endurance limit is crucial. From aerospace and automotive industries to civil engineering and medical implants, the endurance limit plays a critical role in ensuring the reliability, safety, and longevity of various mechanical systems subjected to cyclic loading.
In conclusion, the endurance limit is an essential concept that engineers and materials scientists must consider when designing and manufacturing components that experience frequent and fluctuating stress conditions. By incorporating the endurance limit into the design process, industries can optimize performance, enhance safety, reduce costs, and prolong the lifespan of mechanical systems. Continued research and advancements in understanding the endurance limit will lead to improved engineering practices and more reliable and efficient systems in the future.